V-ZUG first began manufacturing its premium appliances in Zug, a satellite town of Zurich, in 1913. The brand is ubiquitous in its home market (it’s estimated that 90% of Swiss households have a V-ZUG appliance) and over the past decade the company has experienced strong international growth from discerning customers around the globe who are drawn to the innovation and craftsmanship of ‘Swiss made’.
But therein lies a dilemma. As the order book increases, how do you increase production on a constrained site? For the Apples and Teslas of the world, you look for somewhere that land and labour are cheap and build a sprawling, behemoth of a warehouse. For a company that shares the name of the town in which its based, in a country that it leverages for its national reputation for quality, that was never going to be an option. Instead, and with typical V-ZUG thoughtfulness and ingenuity, they developed a masterplan for success and have executed it to perfection.
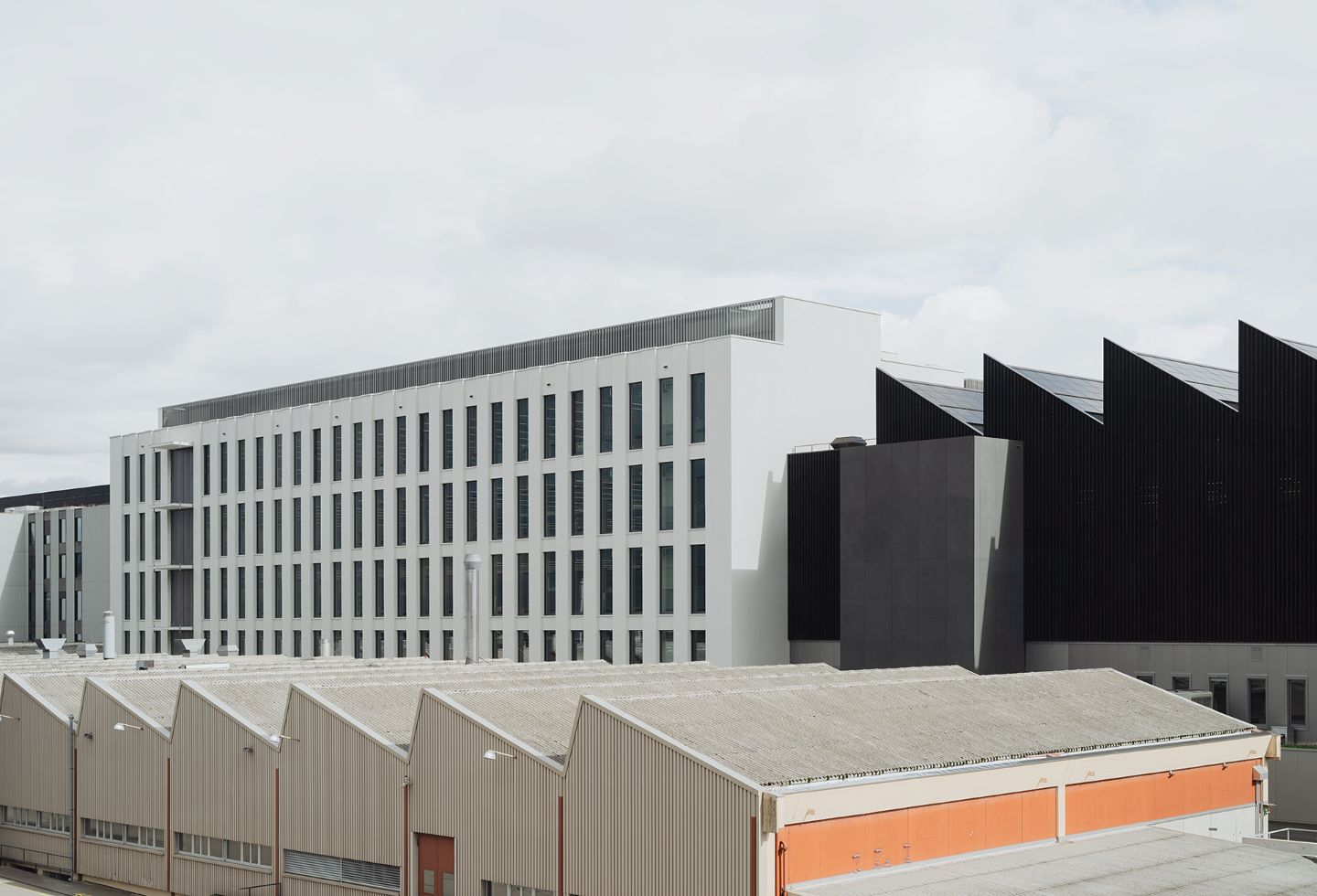
The Zug 2033 site transformation has involved taking the original V-ZUG production site and creating a precinct for the company’s own corporate headquarters, alongside space for sympathetically-aligned business, startups and educational institutions. Which is how the challenge of reducing the footprint of the entire factory came to Chief Operating Officer Adrian Theiler, Head of Industrial Automation Markus Estermann and architect Michael Roth of Diener & Diener. Together they are pioneering urban manufacturing, and Zephyr Ost, the latest addition on site, is now complete and will soon be home to 200 employees producing the company’s range of ovens, steamers, dishwashers and fabric care appliances.
“This is where we conceive of new products, pursue innovation, develop and produce new products,” explains Theiler. “Zephyr Ost is one of three buildings that – together with Zephyr Hangar and Mistral – showcases V-ZUG’s commitment to verticalizing its factories. As part of our transformation [we have] invested handsomely in new buildings and production facilities. This will stand us in good stead in the market and ensure we remain competitive.”
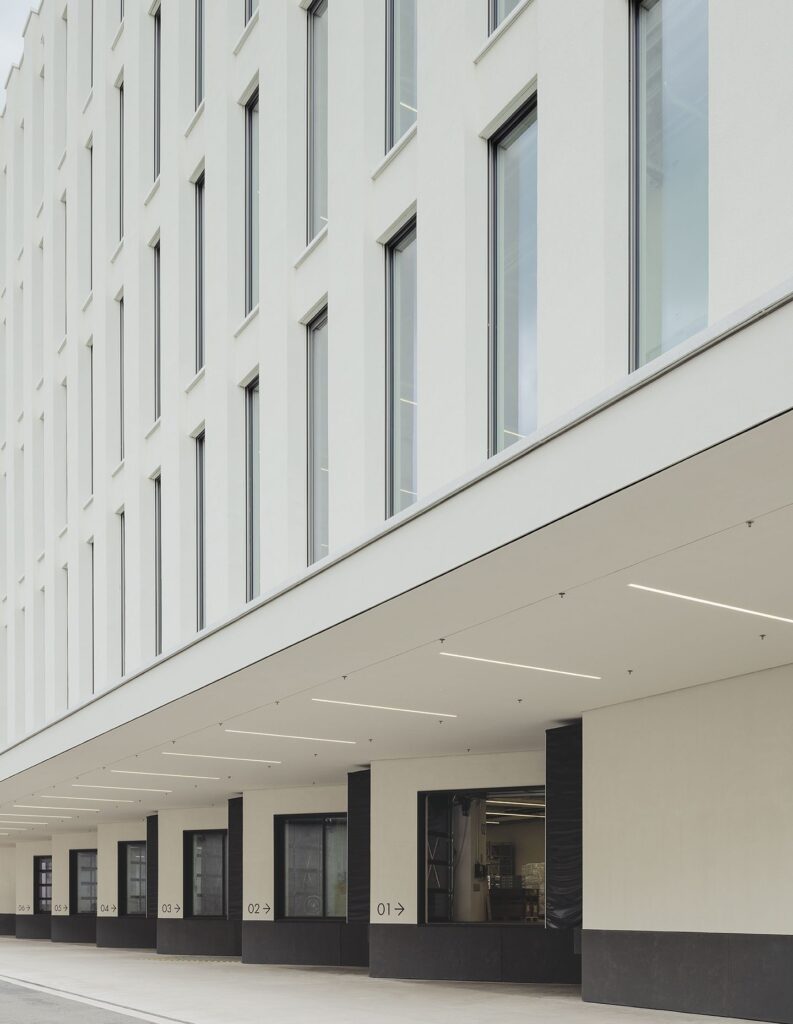
The new generation of products taking shape in these buildings are representative of a new era of manufacturing excellence which considers the various environmental and economic realities the company operates in – as well as the social fabric of its physical location. On the sustainability front the building uses an innovative low-carbon recycled concrete product that also sequesters carbon, has photovoltaics on the roof and taps into the municipality-led Multi Energy Hub to access CO2-neutral energy for heating and cooling. And although the verticalization was footprint-driven, it also has environmental benefits.
“Verticalisation means that the production areas are no longer housed on a single floor; instead they are distributed across different levels,” says Estermann. “In other words, we are building upward, not outward. As well as being more compact, the new production process will therefore be more sustainable.”
A further advantage is that distances are shorter, which in turn helps to optimise processes. Using automated logistics also allows the company to streamline movements: shorter chains lead to higher efficiency.
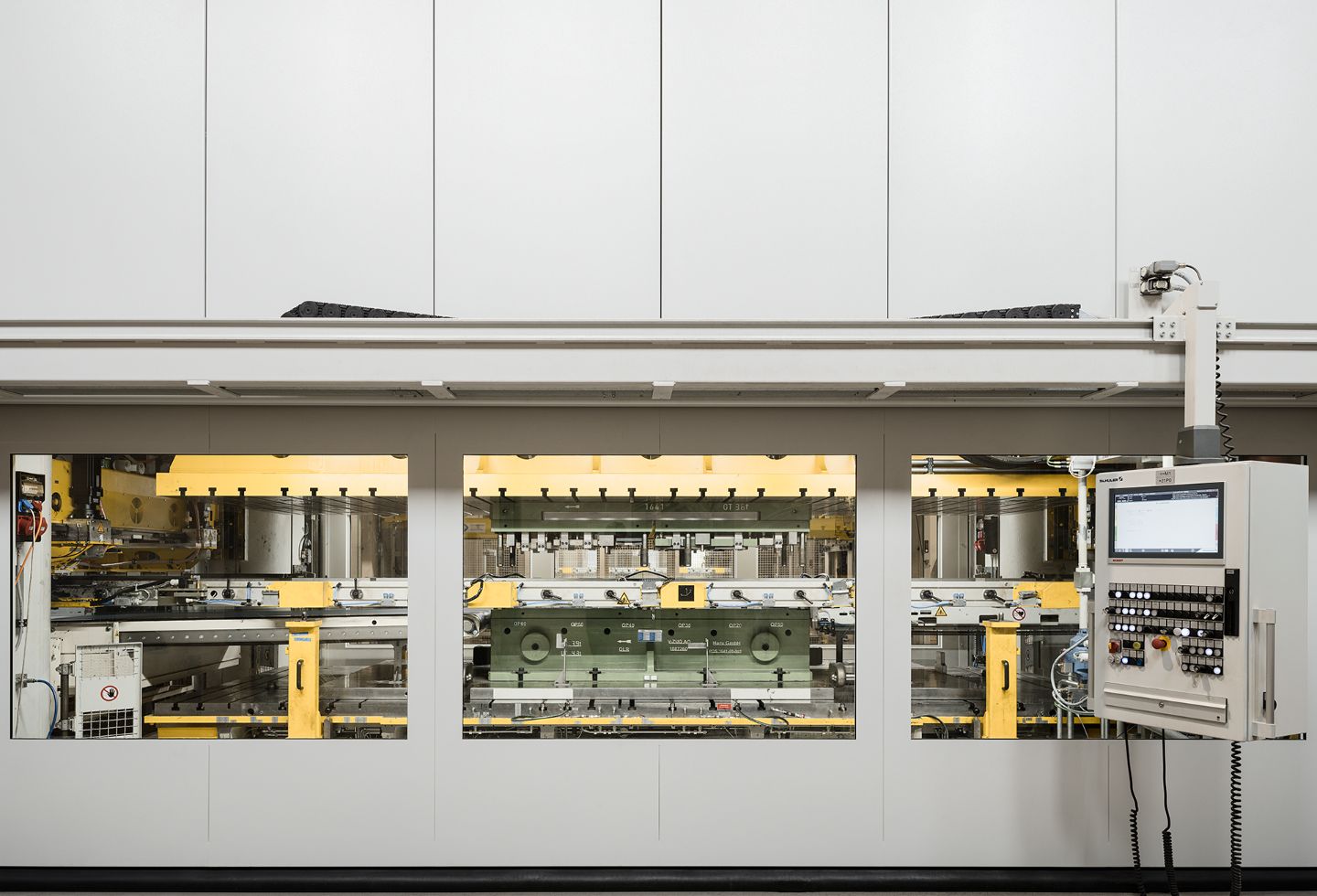
V-ZUG has approached the juggernaut of AI with what it calls ‘human-driven automation’. The company says that while such a vertical factory relies on state-of-the-art automation, humans are still its most important asset. V-ZUG argues that the more complex the automated system, the more crucial the human contribution, because you need outstanding people to design, operate and complement the expert machines that make almost 1300 first-class home appliances every day. They also perform metal work that requires a level of accuracy only a person can achieve. Factory workers are thoroughly trained and required to constantly rotate tasks, an approach that keeps them engaged and ultimately increases the quality of their work.”
Creating a building fit for a highly skilled and highly valued workforce was front of mind for the architectural team at Diener & Diener, who also designed Zephyr Hangar.
“This is a place of work, so it was imperative to make it as attractive as possible, while offering all the conveniences an employee could need,” says Roth. “We think that having rooms filled with daylight and expansive views is an excellent way to make this a good place to work.”
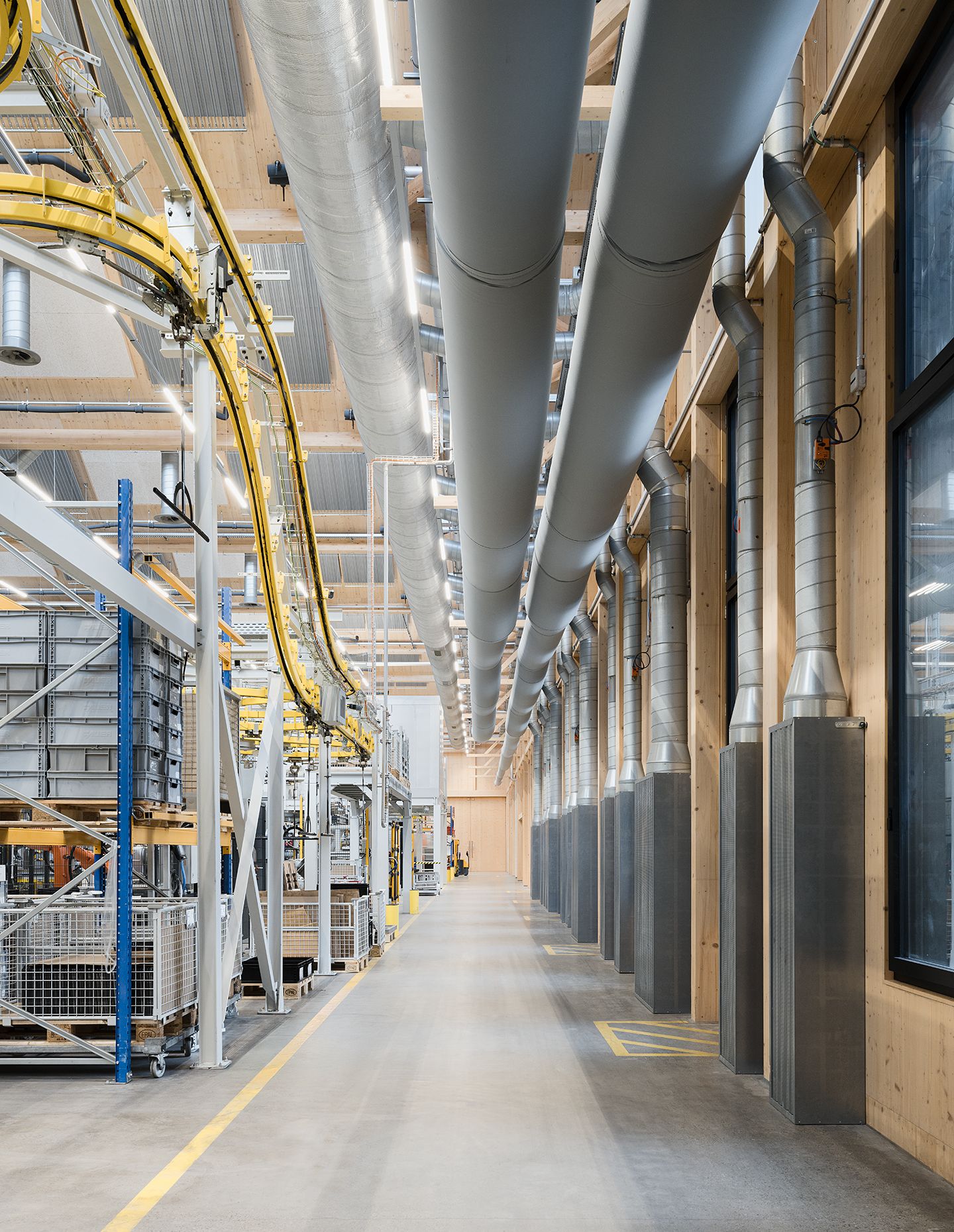
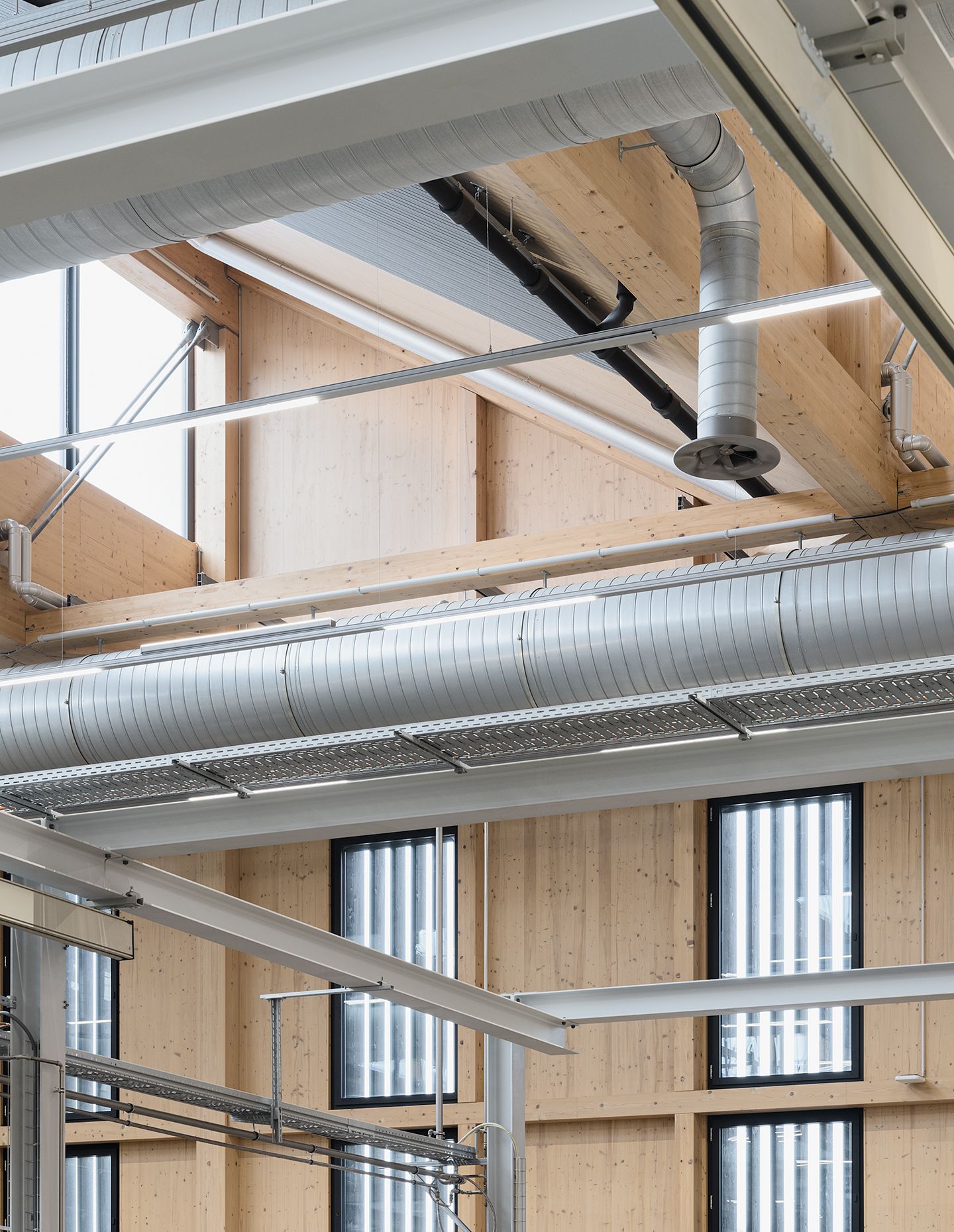
Lightwells through the 6-storey building provide the employees with natural light as well as spaces for outdoor enjoyment. Roth was also conscious of the building’s location in the centre of Zug, and giving it a social dimension.
“The major challenge we faced was the sheer size of the building, which is 70 metres in length and 50 metres deep,” continues Roth. “Even so, it doesn’t actually look this big, whether you are viewing it from the surrounding streets or on site. This allows it to fit in seamlessly with the neighbouring districts, where people live, do various jobs, study and enjoy their leisure time.”
With Zephyr Ost complete, V-ZUG is now underway with Zephyr West which will house the company’s corporate offices. Watch this space.